2/12 - 2/15
- Cormac Lynch
- Feb 16, 2024
- 2 min read
This week I worked more on the light for the soldering station. I started off on Monday by finishing the design for the bracket that goes on the bottom of the light. The two slots on the left and right sides are designed for putting magnets in, which will hold it onto the magnetic bottom of the light. The hole in the middle is designed for screwing a gooseneck pipe into.
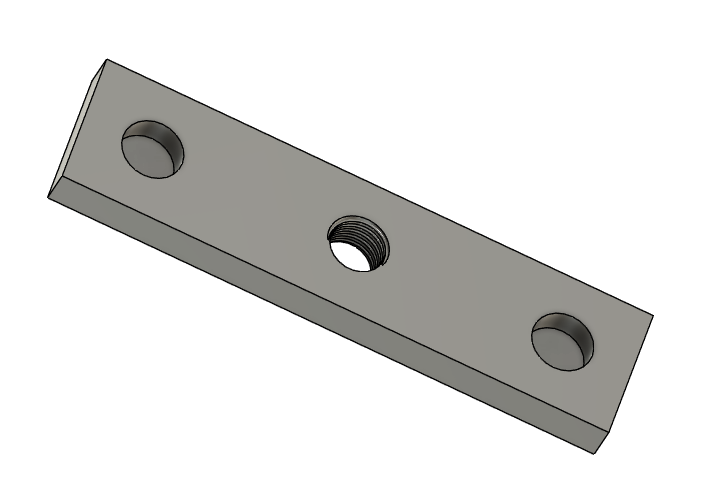
After ensuring that they were the right size, I printed a model of the bracket using the 3D printer. This however, came with some problems of its own, that being that the slots for the magnets, while they were the right size when I laser cut them out of cardboard, I didn't account for the fact that the 3D printer can sometimes print holes as smaller than they actually should be, and that cardboard is much easy to fit something that's too big into it.
I fixed this problem by deciding to use the mill to create the bracket, which would not only be more effective for the design I have, but also because I can thread the middle hole, making it easier to screw the gooseneck piping into it. First of all though, I had to make sure I had the right size for all the holes this time. So with the help of my teacher Mr. Lewkowitz, we did a test cut of the hole to make sure the size was right. Also wanting to make sure that the threaded hole would be the right size, I tried to check the mill's chart for the threading size. to make sure I cut the right size hole for the same threading of the gooseneck. However the size 10mm x 1 wasn't on there, and before I could find it online, I ran out of time, so when I come back from February Break, I'll resume this.
Comments